Pengecoran cetakan cangkangadalah proses dimana pasir yang bercampur dengan resin thermosetting dibiarkan bersentuhan dengan plat pola metalik yang dipanaskan, sehingga terbentuklah cangkang yang tipis dan kuat disekitar pola tersebut. Kemudian cangkang dikeluarkan dari pola dan penutup serta tarikan dilepas bersama-sama dan disimpan dalam labu dengan bahan cadangan yang diperlukan dan logam cair dituangkan ke dalam cetakan.
Umumnya pasir kering dan halus (90 sampai 140 GFN) yang benar-benar bebas dari lempung digunakan untuk pembuatan pasir cetakan cangkang. Ukuran butir yang akan dipilih tergantung pada permukaan akhir yang diinginkan pada pengecoran. Ukuran butiran yang terlalu halus membutuhkan resin dalam jumlah besar, yang membuat cetakan mahal.
Resin sintetis yang digunakan dalam cetakan cangkang pada dasarnya adalah resin termoseting, yang mengeras secara permanen oleh panas. Resin yang paling banyak digunakan adalah resin fenol formaldehida. Dikombinasikan dengan pasir, mereka memiliki kekuatan dan ketahanan yang sangat tinggi terhadap panas. Resin fenolik yang digunakan dalam pencetakan cangkang biasanya terdiri dari dua tahap, yaitu resin memiliki kelebihan fenol dan bertindak seperti bahan termoplastik. Selama pelapisan dengan pasir, resin digabungkan dengan katalis seperti heksa metilen tetramina (heksa) dalam proporsi sekitar 14 hingga 16% sehingga mengembangkan karakteristik termoseting. Temperatur pengeringan untuk ini akan menjadi sekitar 150 C dan waktu yang dibutuhkan adalah 50 sampai 60 detik.
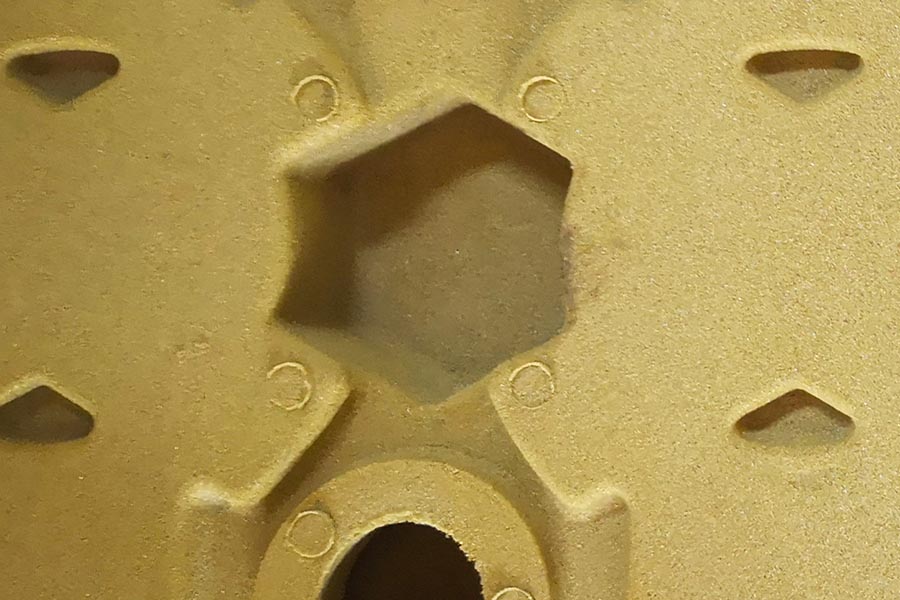
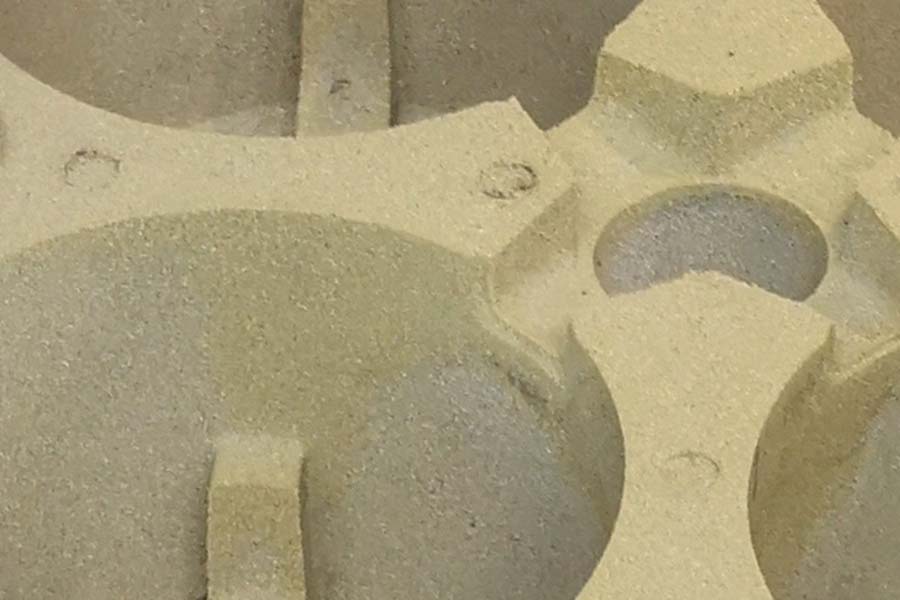
Keuntungan dari Proses Pengecoran Cetakan Shell
1. Coran cetakan cangkang umumnya lebih akurat secara dimensi daripada pengecoran pasir. Toleransi +0.25 mm untuk pengecoran baja dan +0 dapat diperoleh. 35 mm untuk pengecoran besi cor kelabu dalam kondisi kerja normal. Dalam kasus cetakan cangkang yang ditoleransi dengan ketat, seseorang dapat memperolehnya dalam kisaran +0,03 hingga +0,13 mm untuk aplikasi tertentu.
2. Permukaan yang lebih halus dapat diperoleh pada coran kerang. Ini terutama dicapai dengan butiran ukuran yang lebih halus yang digunakan. Kisaran kekasaran yang khas adalah dari urutan 3 sampai 6 mircron.
3. Sudut rancangan, yang lebih rendah dari pada cetakan pasir, diperlukan dalam cetakan cangkang. Pengurangan sudut draft mungkin dari 50 hingga 75%, yang sangat menghemat biaya material dan biaya pemesinan selanjutnya.
4. Terkadang, inti khusus dapat dihilangkan dalam cetakan cangkang. Karena pasir memiliki kekuatan yang tinggi maka cetakan dapat dirancang sedemikian rupa sehingga rongga bagian dalam dapat dibentuk langsung dengan kebutuhan inti cangkang.
5. Juga, bagian yang sangat tipis (hingga 0,25 mm) dari jenis kepala silinder berpendingin udara dapat dengan mudah dibuat oleh cetakan cangkang karena kekuatan pasir yang lebih tinggi yang digunakan untuk pencetakan.
6. Permeabilitas cangkang tinggi dan karena itu tidak terjadi inklusi gas.
7. Jumlah pasir yang harus digunakan sangat sedikit.
8. Mekanisasi mudah dilakukan karena proses sederhana yang terlibat dalam pencetakan cangkang.
Keterbatasan Proses Pengecoran Cetakan Shell
1. Pattens sangat mahal dan karena itu ekonomis hanya jika digunakan dalam produksi skala besar. Dalam aplikasi tipikal, cetakan cangkang menjadi lebih ekonomis daripada cetakan pasir jika keluaran yang dibutuhkan di atas 15000 buah karena biaya pola yang lebih tinggi.
2. Ukuran pengecoran yang diperoleh dengan cetakan cangkang dibatasi. Umumnya, pengecoran dengan berat hingga 200 kg dapat dilakukan, meskipun dalam jumlah yang lebih kecil, tuang hingga berat 450 kg dapat dilakukan.
3. Bentuk yang sangat rumit tidak dapat diperoleh.
4. Peralatan yang lebih canggih dibutuhkan untuk menangani cetakan cangkang seperti yang diperlukan untuk pola logam yang dipanaskan.
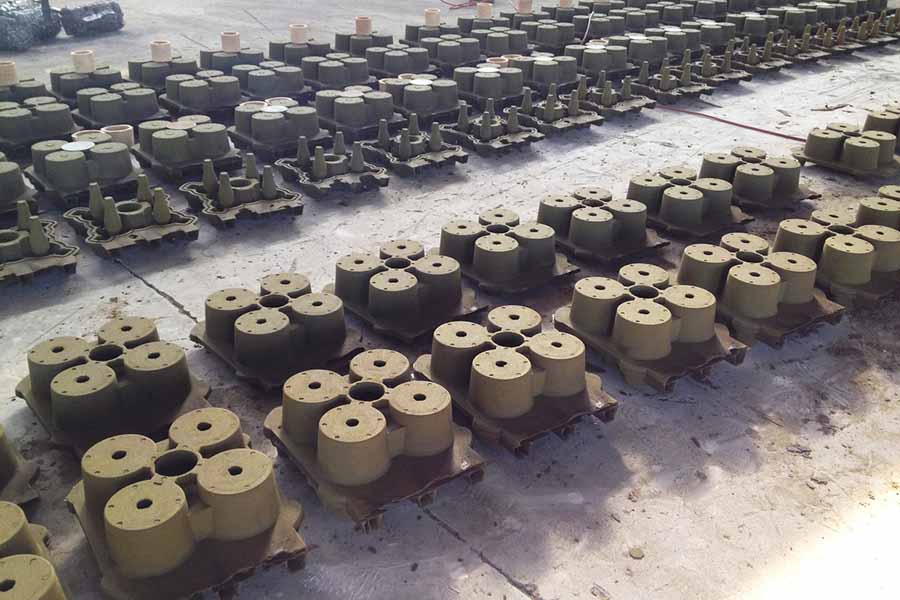
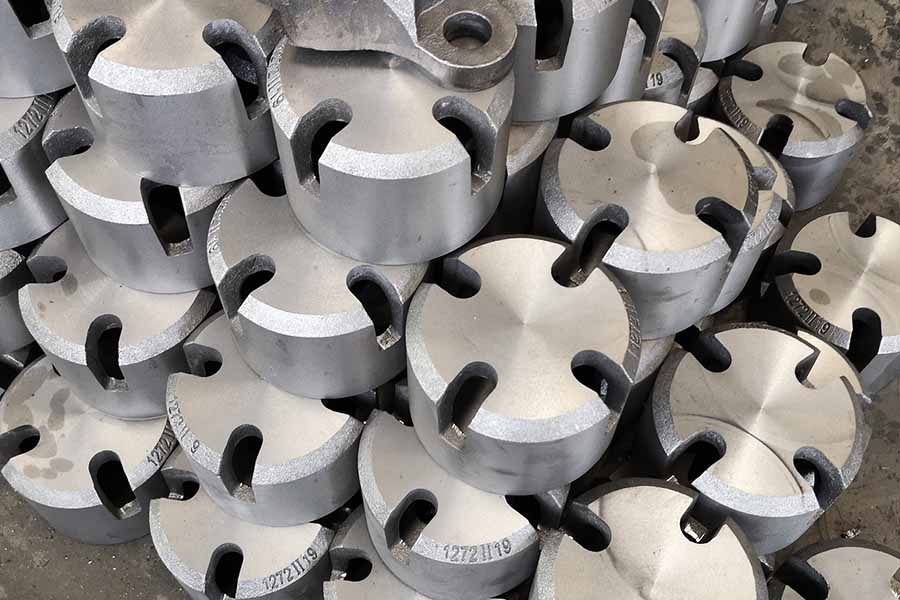
Waktu posting: Des-25-2020