Sebagai proses manufaktur dasar dengan sejarah 6000 tahun, teknologi pengecoran tidak hanya memiliki sejarah panjang, tetapi pada saat yang sama telah menyerap teknologi baru, material baru, dan proses baru yang dikembangkan dalam sains modern pada waktunya. Kami memiliki tanggung jawab untuk memajukan industri manufaktur dasar ini. Poin-poin berikut ini adalah beberapa pemikiran kami untuk tren perkembangan proses pengecoran pasir ke depan.
1 Teknologi pengecoran berkembang menuju penghematan energi dan penghematan material
Dalam proses produksi pengecoran, sejumlah besar energi dikonsumsi dalam proses peleburan logam. Di saat yang sama, permintaan bahan habis pakai dalam proses pengecoran pasir juga besar. Oleh karena itu, bagaimana cara lebih menghemat energi dan material merupakan masalah utama yang dihadapi pabrik pengecoran pasir. Pengukuran yang umum digunakan terutama meliputi:
1) Mengadopsi cetakan pasir canggih, teknologi dan peralatan pembuatan inti. Dalam proses produksi pengecoran pasir, tekanan tinggi, tekanan statis, tekanan injeksi dan peralatan pelubang udara harus digunakan sebanyak mungkin. Dan sejauh mungkin menggunakan pasir yang mengeras sendiri, pengecoran busa yang hilang, pengecoran vakum dan pengecoran khusus (seperti pengecoran investasi, pengecoran cetakan logam) dan teknologi lainnya.
2) Pemulihan pasir dan penggunaan kembali. Saat menuang bagian logam non-ferrous, pengecoran besi dan pengecoran baja, sesuai dengan suhu sintering pasir, tingkat pemulihan pasir tua yang diregenerasi secara mekanis dapat mencapai 90%. Diantaranya, kombinasi daur ulang pasir dan regenerasi basah adalah metode yang paling ideal dan hemat biaya.
3) Daur ulang perekat. Misalnya, jika pengecoran dihilangkan inti dengan metode kering dan perekat tetap berada di pasir, proses yang sesuai dapat membuat perekat digunakan kembali, sehingga sangat mengurangi biaya perekat.
4) Regenerasi cetakan dan bahan cetakan.
2 Lebih sedikit polusi atau bahkan tanpa polusi
Pengecoran pasir menghasilkan banyak limbah cair, gas buang dan debu selama proses produksi. Oleh karena itu, pengecoran bukan hanya rumah tangga yang mengkonsumsi energi besar, tetapi juga sumber polusi yang besar. Terutama di China, polusi di pabrik peleburan lebih serius daripada di negara lain. Diantaranya, debu, udara dan limbah padat yang dibuang dari pabrik pengecoran pasir adalah yang paling serius. Terutama dalam beberapa tahun terakhir, kebijakan perlindungan lingkungan China menjadi semakin ketat, dan pengecoran harus mengambil tindakan efektif untuk mengendalikan polusi. Untuk mencapai produksi pengecoran pasir yang hijau dan bersih, pengikat anorganik hijau harus digunakan sebanyak mungkin, atau kurang atau tidak ada pengikat yang harus digunakan. Di antara proses pengecoran pasir yang saat ini terlibat, pengecoran busa yang hilang, pengecoran proses V dan pengecoran pasir natrium silikat relatif ramah lingkungan. Karena pengecoran busa hilang dan pengecoran proses V menggunakan pemodelan pasir kering yang tidak membutuhkan bahan pengikat, sedangkan pengecoran pasir natrium silikat menggunakan bahan pengikat organik.
3 Akurasi coran dimensi dan geometris yang lebih tinggi
Dengan perkembangan proses pembentukan presisi dari casting blank, akurasi gemometical dan dimensi dari pembentukan bagian berkembang dari pembentukan bentuk jaring dekat menjadi bentuk jaring, yaitu, hampir tidak ada pembentukan margin. Perbedaan antara pengecoran kosong dan bagian yang dibutuhkan semakin kecil dan kecil. Setelah beberapa blank terbentuk, mereka telah mendekati atau mencapai bentuk dan ukuran akhir dari bagian-bagiannya, dan dapat dirakit langsung setelah digiling.
4 Kurang atau tidak ada cacat
Indikator lain dari kekasaran pengecoran dan tingkat pembentukan bagian adalah jumlah, ukuran dan kerusakan cacat pengecoran. Karena proses pengerjaan panas dan pengecoran logam sangat rumit dan dipengaruhi oleh banyak faktor, cacat pengecoran sulit dihindari. Namun, sedikit atau tidak ada cacat yang menjadi tren masa depan. Ada beberapa langkah efektif:
1) Mengadopsi teknologi canggih untuk meningkatkan kepadatan struktur paduan dan meletakkan dasar untuk mendapatkan coran suara.
2) Gunakan perangkat lunak simulasi pengecoran sebelumnya untuk mensimulasikan proses pengecoran aktual dalam tahap desain. Berdasarkan hasil simulasi, desain proses dioptimalkan untuk mewujudkan keberhasilan pencetakan dan uji coba cetakan satu kali.
3) Memperkuat pemantauan proses dan melakukan operasi secara ketat sesuai dengan instruksi operasi yang ditentukan.
4) Perkuat pengujian non-destruktif dalam proses produksi, temukan suku cadang di luar standar tepat waktu dan ambil langkah perbaikan dan perbaikan yang sesuai.
5) Tentukan nilai kerusakan kritis melalui penelitian dan evaluasi keamanan dan keandalan suku cadang.
5 Produksi coran ringan.
Dalam produksi mobil penumpang, truk, dan peralatan transportasi lainnya, cara meminimalkan bobot suku cadang sambil memastikan kekuatan suku cadang merupakan tren yang semakin jelas. Ada dua aspek utama untuk mencapai penurunan berat badan. Salah satunya adalah dengan menggunakan bahan baku ringan, dan yang lainnya adalah untuk mengurangi berat bagian dari desain struktural bagian tersebut. Karena pengecoran pasir memiliki fleksibilitas yang tinggi dalam desain struktural, dan ada juga banyak bahan logam tradisional dan baru untuk dipilih, pengecoran pasir dapat memainkan peran besar dalam produksi ringan.
6 Penerapan teknologi baru seperti pencetakan 3D dalam pembuatan cetakan
Dengan perkembangan dan kematangan teknologi pencetakan 3D, itu juga semakin banyak digunakan di bidang pengecoran. Dibandingkan dengan pengembangan cetakan tradisional, teknologi pencetakan 3D dapat dengan cepat menghasilkan cetakan yang dibutuhkan dengan biaya yang lebih rendah. Sebagai teknologi pembuatan prototipe yang cepat, pencetakan 3D dapat memberikan keuntungan penuh untuk keuntungannya dalam produksi uji coba sampel dan tahap pengecoran dalam jumlah kecil.
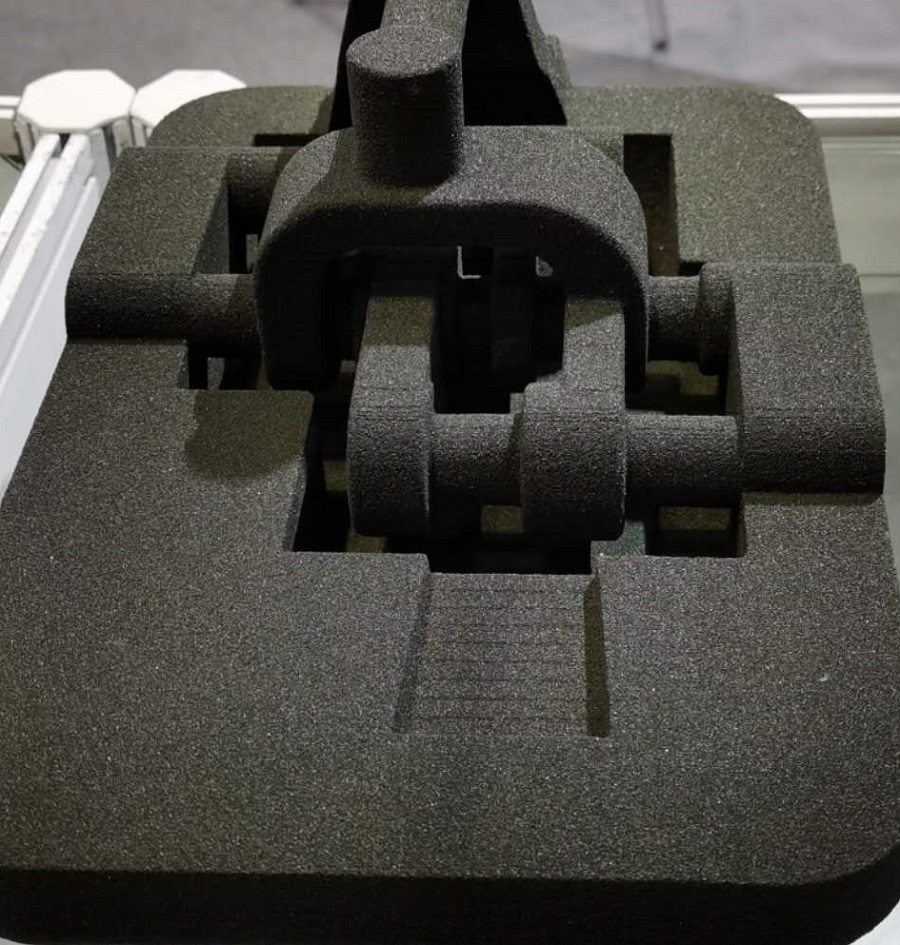
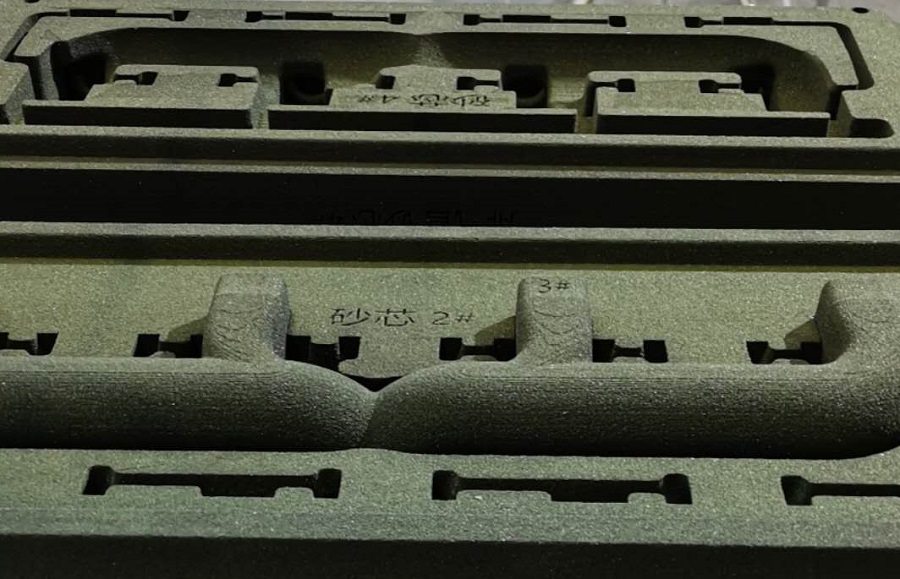
Waktu posting: Des-25-2020