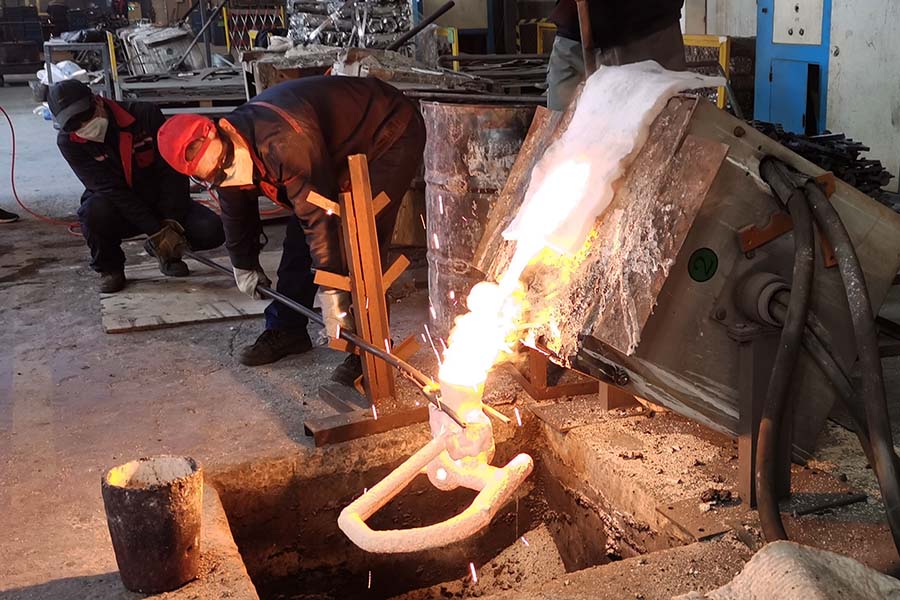
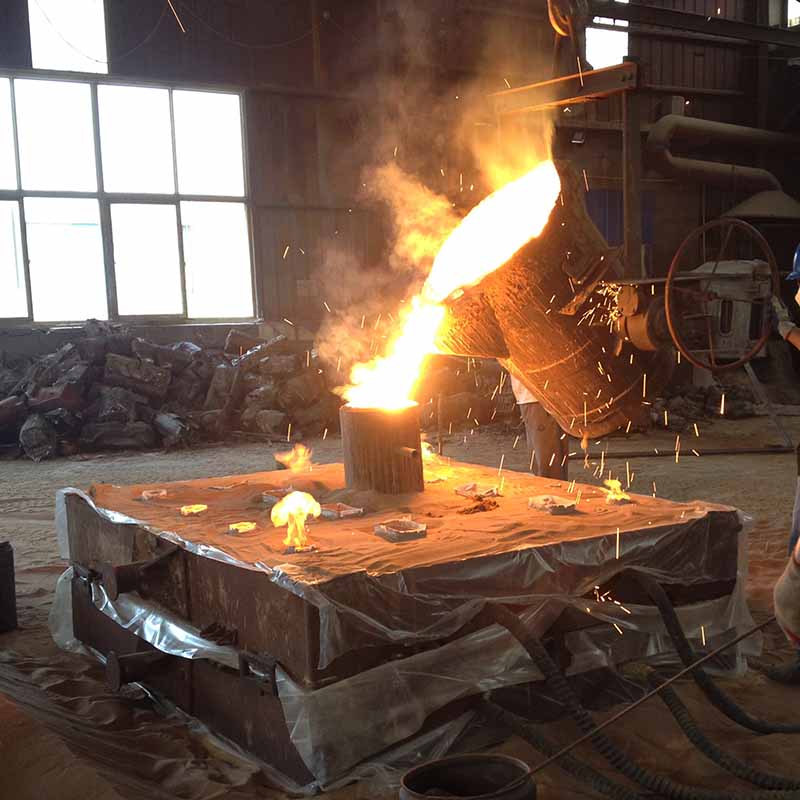
Pengecoran adalah salah satu metode pembentukan logam paling awal yang diketahui manusia. Ini umumnya berarti menuangkan logam cair ke dalam cetakan tahan api dengan rongga sesuai bentuk yang akan dibuat, dan membiarkannya mengeras. KapanSetelah mengeras, benda logam yang diinginkan dikeluarkan dari cetakan tahan api baik dengan cara memecahkan cetakan atau dengan membongkar cetakannya. Benda yang dipadatkan disebut pengecoran. Proses ini disebut juga pendirian, dan disebut pabrik modern yang fokus pada pengecoran bagian logampengecoran.
1. Sejarah Proses Pengecoran
Proses pengecoran kemungkinan ditemukan sekitar tahun 3500 SM di Mesopotamia. Di banyak belahan dunia pada periode itu, kapak tembaga dan benda datar lainnya dibuat dalam cetakan terbuka yang terbuat dari batu atau dipanggang.tanah liat. Cetakan-cetakan ini pada dasarnya utuh. Namun pada masa selanjutnya, ketika benda bulat perlu dibuat, cetakan tersebut dipecah menjadi dua bagian atau lebih untuk memudahkan penarikan benda bulat tersebut.Zaman Perunggu (sekitar tahun 2000 SM) membawa lebih banyak penyempurnaan dalam proses pengecoran. Mungkin untuk pertama kalinya, inti untuk membuat kantong berlubang pada benda ditemukan. Inti ini terbuat dari tanah liat yang dipanggang.Selain itu, proses cire perdue atau lilin hilang banyak digunakan untuk pembuatan ornamen dan pengerjaan halus.
Teknologi pengecoran telah ditingkatkan secara signifikan oleh bangsa Cina sejak sekitar tahun 1500 SM. Sebelumnya, tidak ada bukti adanya aktivitas casting yang ditemukan di Tiongkok. Tampaknya mereka tidak hebatakrab dengan proses cire perdue dan tidak menggunakannya secara luas, melainkan mengkhususkan diri pada cetakan multi-bagian untuk membuat pekerjaan yang sangat rumit. Mereka menghabiskan banyak waktu untuk menyempurnakan cetakan hingga detail terakhir sehingga sulitpekerjaan finishing apa pun diperlukan pada pengecoran yang dibuat dari cetakan. Mereka mungkin membuat cetakan potongan yang berisi potongan-potongan yang dipasang dengan cermat, berjumlah tiga puluh atau lebih. Faktanya, banyak cetakan serupa yang telah digaliselama penggalian arkeologi di berbagai wilayah Tiongkok.
Peradaban Lembah Indus juga dikenal karena penggunaan pengecoran tembaga dan perunggu secara ekstensif untuk ornamen, senjata, perkakas, dan perkakas. Namun tidak banyak kemajuan dalam teknologi. Dari variSelain benda-benda dan patung-patung yang digali dari situs Lembah Indus, mereka tampaknya telah familiar dengan semua metode pengecoran yang diketahui seperti cetakan terbuka, cetakan potongan, dan proses cire perdue.
Meskipun India dapat dikreditkan dengan penemuan baja wadah, tidak banyak penemuan besi yang terlihat di India. Terdapat bukti bahwa pendirian besi telah dimulai sekitar 1000 SM di Suriah dan Persia. Tampaknyaitupengecoran besiTeknologi di India telah digunakan sejak masa invasi Alexander Agung, sekitar 300 SM.
Pilar besi terkenal yang saat ini terletak di dekat minar Qutb di Delhi adalah contoh keterampilan metalurgi orang India kuno. Panjangnya 7,2 m dan terbuat dari besi murni yang dapat ditempa. Hal ini diasumsikan berasal dariperiode Chandragupta II (375-413 M) dari Dinasti Gupta. Tingkat karat pada pilar ini, yang berdiri di luar di udara terbuka praktis nol dan bahkan bagian yang terkubur pun berkarat dengan kecepatan yang sangat lambat. Iniharus dicor terlebih dahulu lalu dipalu hingga menjadi bentuk akhir.
2. Kelebihan dan Keterbatasan
Proses pengecoran banyak digunakan dalam bidang manufaktur karena banyak keuntungannya. Bahan cair mengalir ke bagian kecil mana pun di rongga cetakan dan dengan demikian, segala bentuk rumit – internalatau eksternal – dapat dibuat dengan proses pengecoran. Dimungkinkan untuk mencetak hampir semua material baik itu besi atau non-besi. Selain itu, peralatan yang diperlukan untuk pengecoran cetakan sangat sederhana danmurah. Oleh karena itu, untuk produksi percobaan atau produksi dalam jumlah kecil, ini adalah metode yang ideal. Dalam proses pengecoran, dimungkinkan untuk menempatkan jumlah material tepat pada tempat yang dibutuhkan. Sebagai akibatpengurangan berat dalam desain dapat dicapai.castingumumnya didinginkan secara seragam dari semua sisi dan oleh karena itu diharapkan tidak memiliki sifat terarah. Ada logam dan paduan tertentuyang hanya dapat diproses dengan pengecoran dan bukan dengan proses lain seperti penempaan karena pertimbangan metalurgi. Pengecoran dengan berbagai ukuran dan berat, bahkan hingga 200 ton dapat dibuat.
Namun, keakuratan dimensi dan penyelesaian permukaan dicapai normalproses pengecoran pasirdalam banyak kasus tidak akan cukup untuk penerapan akhir. Untuk mempertimbangkan kasus ini, beberapa casting khususproses seperti diecasting telah dikembangkan, rinciannya diberikan di bab selanjutnya. Selain itu, proses pengecoran pasir sampai batas tertentu memerlukan banyak tenaga kerja dan oleh karena itu banyak perbaikan yang ditujukan untuk hal tersebut,seperti mesin cetak dan mekanisasi pengecoran. Pada beberapa bahan seringkali sulit untuk menghilangkan cacat yang timbul akibat kelembaban yang ada di dalamnyapengecoran pasir.
3. Ketentuan Pengecoran
Pada bab-bab berikutnya akan dijelaskan secara rinci pengecoran pasir, yang merupakan proses dasar pengecoran. Sebelum masuk ke rincian proses, tentukan sejumlah kosakata pengecoran katasesuai.
Labu– Labu cetakan adalah labu yang menahan cetakan pasir tetap utuh. Tergantung pada posisi labu dalam struktur cetakan, labu ini disebut dengan berbagai nama seperti drag, cop, dan pipi. Itu terbuat dari kayuuntuk aplikasi sementara atau lebih umum dari logam untuk penggunaan jangka panjang.
Menyeret– Labu cetakan bawah
Mengatasi– Labu cetakan atas
Pipi– Labu cetakan perantara yang digunakan dalam cetakan tiga bagian.
Pola– Pola merupakan replika dari objek akhir yang akan dibuat dengan beberapa modifikasi. Rongga cetakan dibuat dengan bantuan pola.
Garis perpisahan– Ini adalah garis pemisah antara dua labu cetakan yang membentuk cetakan pasir. Pada pola split, garis ini juga merupakan garis pemisah antara dua bagian pola
Papan Bawah– Ini adalah papan yang biasanya terbuat dari kayu, yang digunakan pada awal pembuatan cetakan. Polanya disimpan terlebih dahulu di papan bawah, ditaburkan pasir di atasnya, kemudian dilakukan serudukan di drag.
Menghadapi Pasir– Sejumlah kecil bahan berkarbon ditaburkan pada permukaan bagian dalam rongga cetakan untuk memberikan permukaan akhir yang lebih baik pada coran
Cetakan Pasir– Ini adalah bahan tahan api yang baru disiapkan yang digunakan untuk membuat rongga cetakan. Ini adalah campuran tanah liat silika dan kelembaban dalam proporsi yang tepat untuk mendapatkan hasil yang diinginkan dan mengelilinginyapola saat membuat cetakan.
Sandaran Pasir– Ini merupakan sebagian besar bahan tahan api yang ditemukan dalam cetakan. Ini terdiri dari pasir bekas dan terbakar.
Inti– Digunakan untuk membuat rongga berongga pada coran.
Menuangkan Baskom– Rongga kecil berbentuk corong di bagian atas cetakan tempat logam cair dituangkan.
Spure– Jalur dimana logam cair dari wadah penuangan mencapai rongga cetakan. Dalam banyak kasus, ia mengontrol aliran logam ke dalam cetakan.
Pelari– Jalur pada bidang perpisahan yang dilalui aliran logam cair sebelum mencapai rongga cetakan.
Gerbang– Titik masuk aktual logam cair memasuki rongga cetakan.
Tasbih– Chaplet digunakan untuk menopang inti di dalam rongga cetakan untuk menjaga beratnya sendiri dan mengatasi gaya metalostatik.
Santai– Pendingin adalah benda logam yang ditempatkan dalam cetakan untuk meningkatkan laju pendinginan coran guna menghasilkan laju pendinginan yang seragam atau diinginkan.
Anak tangga– Merupakan penampung logam cair yang disediakan dalam pengecoran agar logam panas dapat mengalir kembali ke dalam rongga cetakan bila terjadi pengurangan volume logam akibat pemadatan
4. Tata Cara Pembuatan Cetakan Pasir
Tata cara pembuatan cetakan pasir pada umumnya dijelaskan pada langkah-langkah sebagai berikut:
Pertama, papan bawah ditempatkan di platform cetakan atau di lantai, sehingga permukaannya rata. Labu cetakan tarik disimpan terbalik di papan bawah bersama dengan bagian tariknyapola di tengah labu di papan. Harus ada jarak yang cukup antara pola dan dinding labu antara 50 hingga 100 mm. Pasir kering yang menghadap ditaburkanpapan dan pola untuk memberikan lapisan antilengket. Pasir cetakan yang baru disiapkan dengan kualitas yang diperlukan sekarang dituangkan ke dalam drag dan pola hingga ketebalan 30 sampai 50 mm. Sisa dari labu penarik adalahterisi penuh dengan pasir cadangan dan ditabrak secara merata untuk memadatkan pasir. Serbuk pasir harus dilakukan dengan benar agar tidak memadatkannya terlalu keras sehingga menyulitkan keluarnya gas,juga tidak terlalu longgar, sehingga cetakan tidak mempunyai kekuatan yang cukup. Setelah serudukan selesai, kelebihan pasir di dalam labu dikikis seluruhnya dengan menggunakan batang datar hingga setinggi tepi labu.
Nah, dengan kawat ventilasi, yaitu kawat berdiameter 1 sampai 2 mm dengan ujung runcing, lubang ventilasi dibuat di tarik hingga seluruh kedalaman labu serta sesuai pola untuk memudahkan pembuangan gas. selama castingpemadatan. Ini menyelesaikan persiapan drag.
Labu penarik yang telah selesai sekarang digulingkan ke papan bawah sehingga memperlihatkan pola seperti yang ditunjukkan dalam foto. Dengan menggunakan licin, tepi pasir di sekitar pola diperbaiki dan separuh pola ditempatkan di atasnyapola tarik, sejajarkan dengan bantuan pin dowel. Labu penahan di atas drag terletak sejajar lagi dengan bantuan pin. Pasir perpisahan yang kering ditaburkan di seluruh tarikan dan pola.
Pin sariawan untuk membuat saluran sariawan terletak pada jarak kecil sekitar 50 mm dari pola. Selain itu, pin ariser jika diperlukan disimpan di tempat yang sesuai dan pasir cetakan yang baru disiapkan serupa dengan itutarikan bersama dengan pasir pendukung ditaburkan. Pasir dipadatkan secara menyeluruh, kelebihan pasir dikikis dan lubang ventilasi dibuat di seluruh bagian dalam cop seperti pada drag.
Pin sariawan dan pin e riser ditarik dengan hati-hati dari labu. Nantinya, baskom tuang dipotong di dekat bagian atas sariawan. Cope dipisahkan dari drag dan pasir lepas pada antarmuka cope dan draggaya hambatnya diledakkan dengan bantuan hembusan. Sekarang, bagian cop dan drag pattern ditarik dengan menggunakan draw spike dan mengetuk seluruh pola untuk sedikit memperbesar rongga cetakan sehinggadinding cetakan tidak rusak oleh pola penarikan. Pelari dan gerbang dipotong dalam cetakan dengan hati-hati tanpa merusak cetakan. Pasir berlebih atau lepas yang ditemukan di pelari dan rongga cetakan akan tertiuppergi menggunakan bellow. Sekarang, pasir yang menghadap dalam bentuk pasta diaplikasikan ke seluruh rongga cetakan dan pelari, yang akan memberikan hasil akhir permukaan yang baik pada hasil pengecoran.
Inti pasir kering dibuat menggunakan kotak inti. Setelah matang, dimasukkan ke dalam rongga cetakan seperti terlihat pada foto. Cope diganti pada drag dengan menjaga keselarasan keduanya melaluipin. Berat yang sesuai disimpan pada pegangan untuk menjaga gaya metalostatik ke atas selama penuangan logam cair. Cetakan sekarang, seperti terlihat pada foto, siap untuk dituang.
Waktu posting: 25 Des-2020